The desire for energy security and (lack of) climate change are driving two
avenues of innovation to power the next generation of vehicles. The first avenue
is to invent new fuels, such as bio-fuels, that change the supply dynamics of
the industry. The second avenue is to invent entirely new engine concepts to
improve efficiency. One such concept, using
detonations (as opposed to
deflagrations) to combust fuel and
air mixtures, has been investigated since the
1940’s.
Using detonations allows for much higher efficiency engine operation. One of the
most common types of detonation engines is the Pulsed Detonation Engine (PDE).
Unfortunately, due to many difficulties including the intermittent nature of
thrust from such engines, no PDEs have been commercially produced to date
(although the concept has flown in an Air Force test plane).
In a recent review paper, Kailasanath has discussed the history and current work
on a similar detonation engine concept, called a Rotating Detonation Engine
(RDE). An RDE is a similar concept to a PDE in that it uses detonation to burn
the fuel and air, but the RDE offers some advantages over the PDE, primarily
that the detonation is continuous in an RDE. This means that an RDE can generate
thrust continuously instead of intermittently. In addition, the continuous
operation of an RDE allows it to have higher efficiency than a PDE.
A typical PDE is not much more complex than a cylinder containing a combustion
chamber, into which fuel and air are fed, an ignitor and a nozzle to generate
thrust. The fuel and air are pulsed into the combustion chamber, ignited into a
detonation, and expanded through the nozzle, with the detonation traveling along
the long axis of the cylinder. An RDE, by contrast, is more complex. A typical
RDE configuration is a ring-shaped cylinder, where fuel is fed from one end of
the cylinder and a nozzle is at the other end of the cylinder. The detonation
wave travels tangentially around the cylinder, burning the fuel and air as they
are fed into the ring. At the other end of the chamber, the gases are expanded
through the nozzle to generate thrust. This is different from a PDE, where the
detonation wave travels from the front of the cylinder to the back along the
long axis, while in the RDE the detonation wave travels circumferentially around
the cylinder. The following pair of images shows the difference between the
operation of each type of engine. It is important to note that the Rotating or
Pulsed indicates the nature of the combustion wave - not the rotation of parts
in the engine.
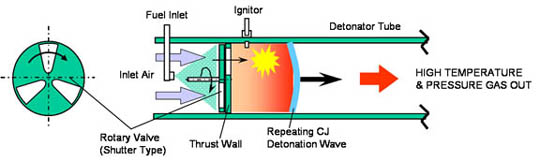
Example Schematic of a Pulse Detonation Engine. Source: UCLA Energy and Propulsion Research Laboratory
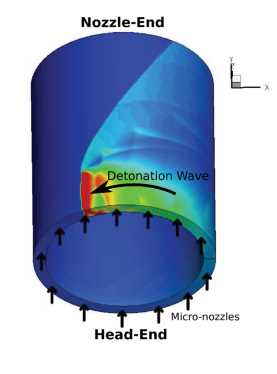
Example schematic of a Rotating Detonation Engine. Source: Kailasanath
According to Kailasanath, research into RDE’s began in the late 1950’s and early
1960’s, and focused primarily on application of RDE’s to rocket propulsion. More
recent research has extended the usefulness of RDE’s to air-breathing propulsion
(i.e. jet-engine-like propulsion). In addition to this experimental work, other
recent work has focused on modeling RDE’s using computer code. These computer
simulations have been used to investigate the overall flow field in an RDE as
well as the performance of an RDE as various engine operating parameters are varied.
Two of the primary control parameters available to experimenters (and the
parameters that are varied in the simulations mentioned above) are the pressure
of the fuel and the air at the inlet, and the pressure at the nozzle end of the
engine, called the inlet pressure and back pressure respectively. Because of the
conditions in the combustion chamber of a detonation engine, the mass flow rate
of the fuel and air mixture through the engine depends only on the inlet
pressure (and not on the back pressure), but the thrust of the engine depends on
both parameters. Interestingly, the specific impulse (a measure of the
efficiency of the engine) depends only on the ratio of the inlet and back
pressures, but not on specific values of either parameter. The maximum value of
specific impulse achieved in this study was about 33% higher than a comparable
PDE, confirming the advantages that RDE’s should have over PDE’s. The author
concludes by noting that the value of specific impulse computed in their study
is quite close to the theoretical ideal efficiency, and further optimizations of
the engine may allow the RDE to get even closer to the theoretical maximum.
Citation: K. Kailasanath, “The Rotating-Detonation-Wave Engine Concept : A Brief
Status report,” 49th AIAA Aerospace Sciences Meeting, 2011, Paper
AIAA-2011-0580.