Quasi-One-Dimensional Nozzle Flow¶
Let’s now consider a simple nozzle with varying cross-sectional area. We will neglect the influence of skin friction and heat transfer at the nozzle wall, so that the only way that the flow may change is due to the area change. In this nozzle, the flow is adiabatic and reversible, so the entropy is constant.
Mass Conservation¶
In steady flow, the mass flow rate is given by the integral relationship:
If we further simplify to quasi-one-dimensional flow, and define the \(z\) axis as the flow direction, then the mass flow rate is:
where \(\dot{m}(z)\) is a constant, and the density, area, or velocity may change as a function of axial location. In differential form, this becomes:
At a given station, or axial (\(z\)) location, the mass flow rate can be related to the local flow conditions by using Eqs. (56) and (71):
where \(R = R_u / W\). Using the results from Eqs. (76) and (77), we can write the mass flow rate as:
Momentum Equation¶
The integral form of the momentum equation for a control volume around the nozzle is:
because we are neglecting friction and drag. In the log differential form, this becomes:
Replacing \(\rho/p\) from the ideal gas law, Eq. (56) and multiplying and dividing the second term by \(a^2\), we can write:
Area-Velocity Relation¶
Using Eq. (90) to eliminate the \(dp/p\) term from Eq. (92), we find the area-velocity relation:
This important equation gives us the relationship between Mach number, area change, and velocity change. We make a number of observations from this equation:
If \(M\rightarrow 0\), this tells us that the product of the area and velocity is a constant, which is the continuity equation for incompressible flow.
If \(M < 1\), the first time on the right-hand side of Eq. (93) is negative. This means that if we want the velocity to increase (\(dV > 0\)), then \(dA\) must be negative and the area must decrease. The opposite is also true; if we want velocity to decrease, the area must increase.
On the other hand, if \(M > 1\), the first time on the right-hand side of Eq. (93) is positive. This means that if we want the velocity to increase (\(dV > 0\)), then \(dA\) must be positive and the area must increase. The opposite is also true; if we want velocity to decrease, the area must decrease.
If \(M = 1\), the area must be constant (\(dA = 0\)). We can prove that for flow to accelerate from subsonic to supersonic, or to decelerate flow from supersonic to subsonic, this area must be a minimum.
Area-Mach Number Relation¶
Now let’s return to the nozzle. We will consider a converging-diverging nozzle, since we know that we want to accelerate the flow from subsonic in the combustion chamber to supersonic exit velocity. From the thrust equation, Eq. (25), we know that the thrust is proportional to the nozzle exit velocity, so higher exit velocities will provide more thrust.
The location of the smallest area in the nozzle is called the throat. Since the area is at a minimum at this location, the slope must be zero, \(dA = 0\). Therefore, the Mach number \(M = 1\), and this defines the characteristic area, \(A^*\).
Let’s apply the conservation equations from a point upstream of the throat to the throat. Then:
Next, multiply and divide the right side by \(\rho_t\). This gives us the relationship of \(\rho_t/\rho\) and \(\rho^*/\rho_t\), which we have developed previously. Finally, using Eq. (84), we find:
This is the area-Mach number relation and it is a critically important equation to understand nozzle flows. To help understand why, we will inspect the figure below.
From the graph, we can see two things immediately:
There are no solutions for \(A/A^*\) less than 1.0. In other words, for isentropic flow, the area at any cross section must be greater than or equal to the characteristic area.
There are two values of \(M\) that correspond to a given \(A/A^*\) value, a subsonic and a supersonic solution. The only exception is at the point (1.0, 1.0), where the area is minimum and the flow is exactly sonic.
Assume that a convergent-divergent nozzle looks like the figure below. At the inlet, the area ratio goes to infinity, such that the Mach number goes to zero and the conditions are stagnated. The Mach number cannot be identically zero, because then there’d be no flow. In the case of isentropic flow through the nozzle, the flow will be accelerated through the subsonic Mach numbers, to the sonic condition at the throat, and then continue accelerating to supersonic Mach numbers.
The static pressure and temperature will also experience continuous decreases over the nozzle. At the inlet, the ratio of the static property to the stagnation property is one. At the throat, the ratios take on the values of the static property over the characteristic property.
Note
There is exactly one value of the pressure ratio \(p_e/p_t\) that gives an isentropic acceleration from subsonic to supersonic flow. Under these conditions, the static pressure outside the nozzle must be equal to the static pressure of the flow at the exit plane.
The particular value of \(p_e/p_t\) that gives isentropic acceleration depends on the expansion ratio of the nozzle, \(A_e/A^*\).
Effect of Pressure Ratio¶
So, what happens when the pressure ratio over the nozzle is not equal to the value that gives isentropic acceleration? There are a few different cases. The trivial case is that the outlet pressure is equal to the inlet pressure and there is no flow. Not super useful.
Now, imagine reducing the pressure ratio slightly, say to 0.9999. The flow accelerates in the converging section, but for this nozzle it does not reach \(M=1\) at the throat. If the flow does not reach sonic velocity at the throat, the diverging section acts as a diffuser according to Eq. (93), and the flow is subsonic throughout.
Next, imagine that we continue to reduce the pressure ratio. Eventually, the pressure ratio will be at some value such that the sonic velocity is reached in the throat. However, the static pressure at the throat, given by Eq. (87), is lower than the static pressure at the exit. Therefore, the diverging section must act as a diffuser and increase the pressure until the outlet.
This second case is shown in the figure below.
Notice that the Mach number reaches exactly 1.0 at the throat, and the static pressure reaches the value specified by Eq. (87) at the throat. For this particular nozzle, the required pressure ratio to reach sonic flow at the throat is very close to one, approximately \(p_e/p_t = 0.997\). The larger the expansion ratio from throat to exit, the smaller the required pressure difference to produce sonic flow at the throat.
Choked Mass Flow Rate¶
We can calculate the mass flow rate in the nozzle for this exit pressure condition from the continuity equation. It is most convenient to calculate the mass flow rate at the throat:
Now imagine reducing the exit pressure of the nozzle below the value required to obtain sonic flow at the throat. The pressure change is communicated to the rest of the flow by pressure waves that travel at the speed of sound. When the flow reaches the sonic velocity at the throat, downstream pressure changes can no longer be communicated through the throat into the converging section.
Therefore, once sonic flow is reached at the throat, the flow conditions, including the pressure, density, and temperature are fixed no matter what the exit pressure is. Likewise, the conditions in the converging section are fixed (assuming the stagnation conditions are fixed).
From the continuity equation, we see that this results in the mass flow rate becoming constant, regardless of downstream pressure changes! This condition is called choked flow. Under this condition, the only way to change the mass flow rate is to change the upstream conditions in the combustion chamber.
Overexpanded and Underexpanded Flow¶
Nonetheless, we can continue to change the exit static pressure, for instance, if the nozzle is attached to a rocket ascending through the atmosphere. What happens to the flow in the nozzle in this case?
Remember that the pressure of the flow exiting the nozzle must eventually come to equilibrium with the surrounding pressure. As we change the surrounding pressure, these changes are communicated into the nozzle by sound waves. Once the flow is sonic at the throat, the changes are only communicated partway through the nozzle.
At some location in the nozzle, the velocity of the flow balances the upstream motion of the sound waves. At that location, which depends on the pressure ratio, the sound waves coalesce into a normal shock wave. A shock wave is an infinitesimally thin region where the flow undergoes an irreversible process.
Across the shock wave, the static pressure and temperature are increased and the Mach number is decreased to a subsonic value. The irreversible nature of the process means that the total pressure is decreased and the value of \(A^*\) changes across the shock wave as well.
Since the shock wave reduces the Mach number to subsonic values, the remainder of the diverging section downstream of the shock wave functions as a diffuser. This increases the static pressure further until it matches the conditions outside of the exit. An example of this situation is shown in the figure below.
This condition of the nozzle is called overexpanded because the flow in the nozzle expands to a pressure below the outside pressure, and requires a shock wave to increase the pressure. If you could cut off the nozzle just upstream of the shock wave, you would have a perfectly expanded nozzle. However, since the nozzle is longer than that, the flow tries to continue expanding and can’t.
As the downstream pressure decreases further, the shock moves further and further downstream. Eventually, the normal shock will stand exactly at the exit. The pressure ratio that produces this situation is still larger than the pressure ratio that gives isentropic acceleration throughout the nozzle.
Thus, we can still continue reducing the outside pressure and there will continue to be an irreversible shock that is required to adjust the exit pressure to the outside pressure. When the outside pressure is lower than the pressure that gives a normal shock at the exit, the shock will become angled into an oblique shock.
Oblique shock waves cause the flow to turn, which then requires a Prandtl-Meyer expansion fan to turn back to the direction of flight. This pattern repeats in a phenomenon called a shock diamond.
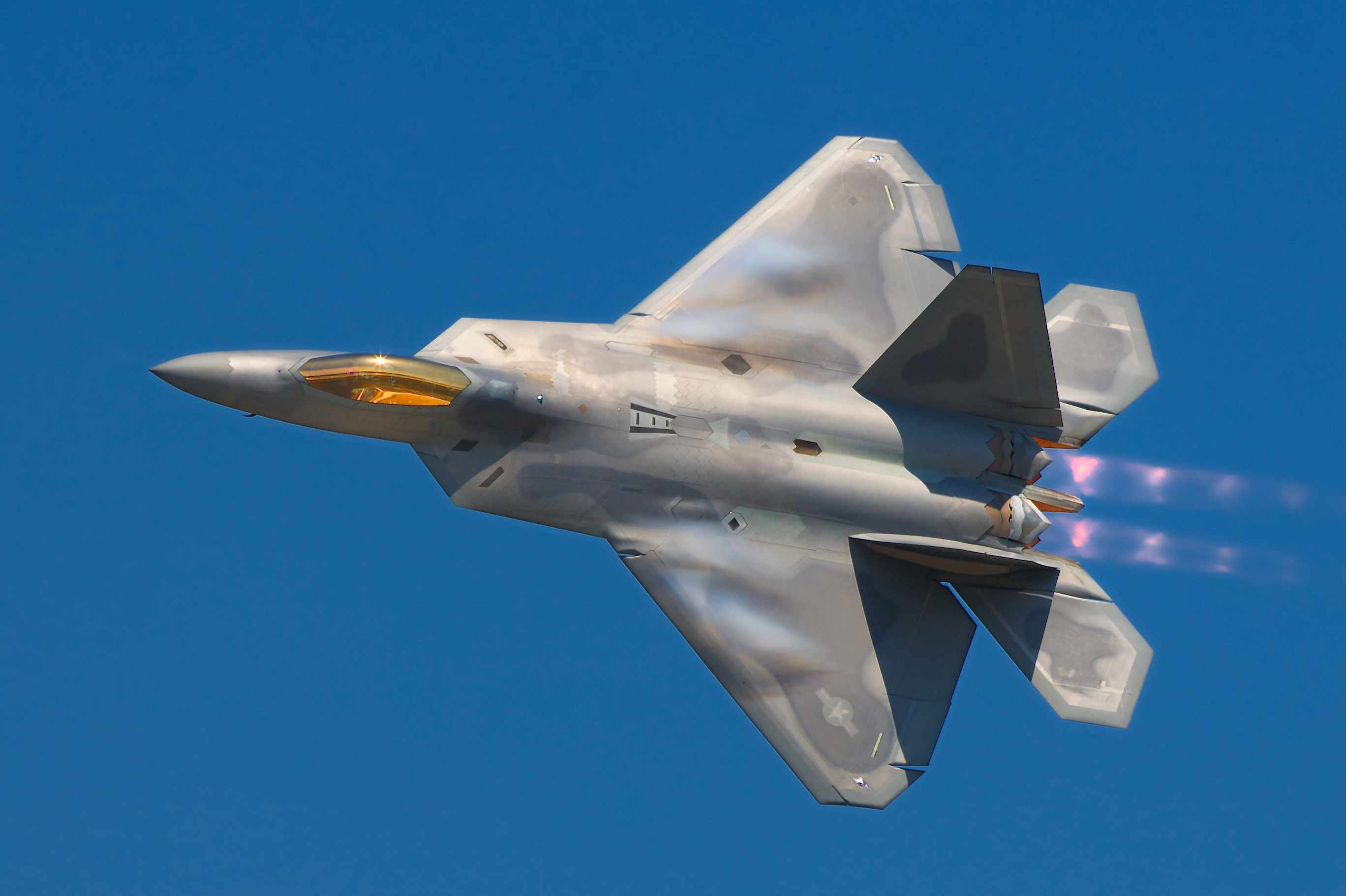
Fig. 10 F-22A Raptor fighter jet with shock diamonds visible in the engine exhaust. Credit: Wikimedia under the CC-BY-SA 2.0 license.¶
Finally, continued reduction of the exterior pressure will result in the ratio \(p_e/p_t\) dropping below the value for isentropic acceleration. In this case, the flow is called underexpanded because the pressure of the flow at the exit plane is higher than the exterior pressure, and it could have been expanded more to match the outside pressure.
To match the exterior pressure, the flow must exit the nozzle through a series of expansion waves to reduce the pressure. These expansion waves turn the flow and to straighten the flow again requires oblique shock waves. Thus, the pattern for underexpanded flow is the same as for overexpanded flow, but it starts with the expansion wave instead of the shock wave.